Tool Application Yamato
TOOL APPLICATION
The diameter adjustment of the tool and the operation parameters to control are easy and flexible. Stock allowance, feed rate and speed are the variables that must be set before starting the operation.
Roller Burnishing does not cause any volume change in the workpiece. But because material is displaced, the diameter will be altered somewhat. In Roller Burnishing of a symmetrical Surface profile, the diameter will change at most by the value of the peek – to – valley height. This must be allowed at the preceding machining operation by leaving enough stock to compensate for the dimensional change.
(Table-1) is to give an idea about determining the stock allowance for the workpieces of different diameters.
Chipless Finishing & Cold Working
Roller Burnishing operation is a chipless finishing method. By the rolling pressure applied to the workpiece surface, the microscopic peaks flow into the valleys in the surface profile. (Figure-3)
Roller burnishing process cold – works metal surfaces to produce a uniform, dense, low micro surface finish. The fact that ROBUTO® does not remove metal – thus does not produce chips – enables the tool to offer a variety of advantages, most of which are not obtainable with other finishing processes such as reaming, boring, and grinding.
The chipless finishing process, roller burnishing cold – works metal under relatively small forces. These forces slightly exceed the yield strength of the material causing a plastic deformation of its surface material. Because the plastic deformation occurs under the recrystallization temperature this process is called cold working.
Minimum Surface Roughness Value (Ra)
In (Table-2), (Ra) values of different materials are listed.
Advantages
Increase in Resistance to Fatigue Failure
Because fatigue failure damages are instantaneous and causes major harm, preventions are necessary. Metals can get cracked even if the forces applied are very small when compared to the yield point. Experience has shown that notches, sharp changes of section and other forms of stress raisers are dangerous to metals in applications involving dynamic forces.
Roller burnishing has an effect of smoothing the profiles of sharp surface imperfections like notches and tool marks. Another and more important point is that the operation of roller burnishing reduces the harmful effects of dynamic forces by forming compressive residual stresses at the surface of workpiece material.
After roller burnishing, at a given depth below the surface, the material is elastically deformed and tries to spring back. This gives rise to compressive stresses at the surface and tensile stresses in the elastically deformed zone. This in turn increases the resistance of the material to fatigue failure, because any external forces must first overcome these residual stresses.
These two major effects of roller burnishing (eliminating the surface imperfections and forming compressive residual stresses) improve the resistance to fatigue failure up to 300%.
Work – Hardening
Roller burnishing compacts and compresses the workpiece metal where it is contacted by the tool. Subsequently, the grain structure is changed and the part becomes strain hardened. Through this granular dislocation and deformation, the grain size is decreased and the boundary volume is increased in the cold worked area.
Because we are dealing with surface hardness, hardness increase cannot be measured by means of Rockwell or Brinell testing. Instead, a method known as Tukon testing is used. Knoop value is obtained from the measurements of Tukon testing. The Knoop Hardness value can be converted to Brinell or Rockwell hardness values.
The Knopp hardness measurement shows a clear hardness increase at the surface, with hardness gradually decreasing to the original value at greater distances from the surface. In Figure-5 the relation of surface hardness and penetration of the hardness (distance from surface) is shown.
Increase in surface hardness for different types of materials is shown in (Table-3)
Corrosion and Porosities
Workpieces that are roller burnished have high resistance to corrosion. Eliminating the pits, scratches and porosities, which could collect reactive substances and contaminants, provides high corrosion resistance.
A workpiece has the risk of cracking when it is under the affect of both reactive substances and tensile residual stresses. Cracking that occurs due to the interaction between static tensile stresses in the metal and a corrosive medium is called stress corrosion cracking. During roller burnishing, these tensile stresses are eliminated when the material is compressed, because compressive residual stresses are formed at the surface of the workpiece.
Roller burnishing successfully removes these factors causing stress corrosion cracking.
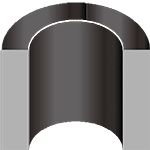
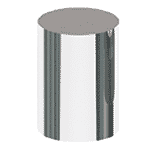
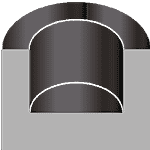
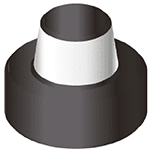
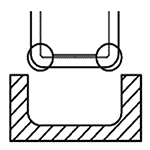
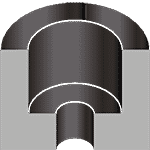
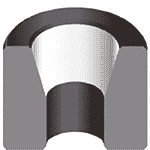
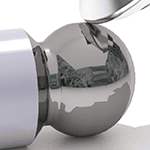
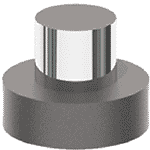
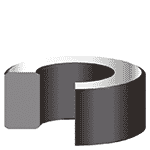
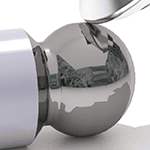
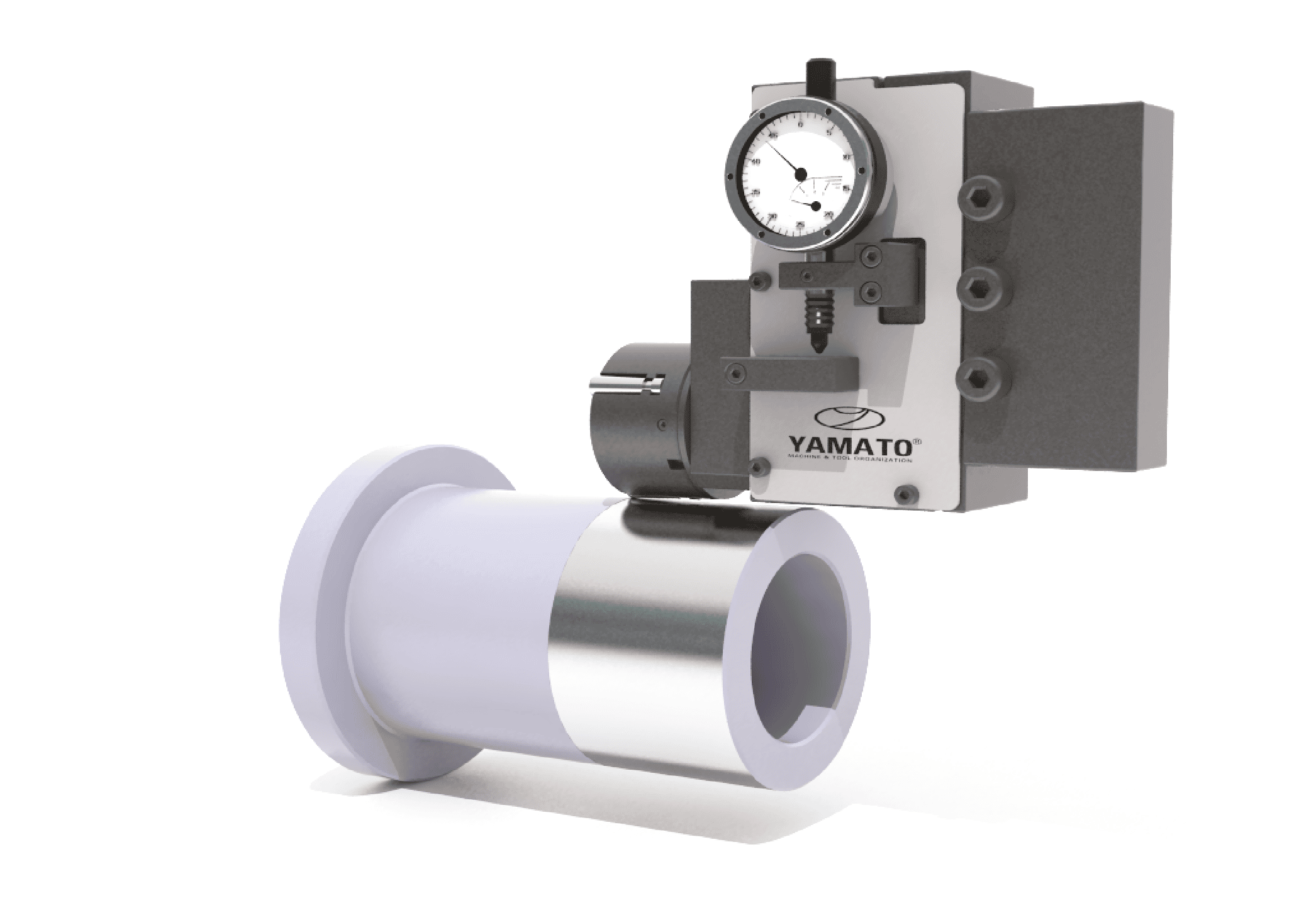

