SKUV API GROOVES Micro hardening and burnishing tools
SKUV API GROOVES Micro hardening and burnishing tools
SOLUTIONS FOR COST-EFFECTIVE AND HIGH QUALITY MACHINING
OF OIL AND GAS SEAL RING GROOVES
SURFACE MICRO HARDENING > LONGER LASTING LOW Ra > BETTER SEALING
Seal ring grooves are critical features on many oil and gas components and require micro hardening on seal surface and a high-quality surface finish. The high component value and complexity make process security essential
MICRO HARDENING
Inconel 625 Before 224 HB > After 300 HB ( 34% increase in hardness)*
Duplex F53 Before 275 HB > After 340 HB ( 24% increase in hardness)*
AISI316 Before 151 HB > After 330 HB (119% increase in hardness)*
A350 LF2 Before 155 HB > After 230 HB ( 48% increase in hardness)*
Elimination of tool marks and minor surface imperfections
Before Burnishing Ra2.0 μm
After Burnishing Ra0.1-0.2 μm
Fast production, at a low cost.. in seconds!
100~150 m/min speed
0.05 – 0.30 mm/rev feed
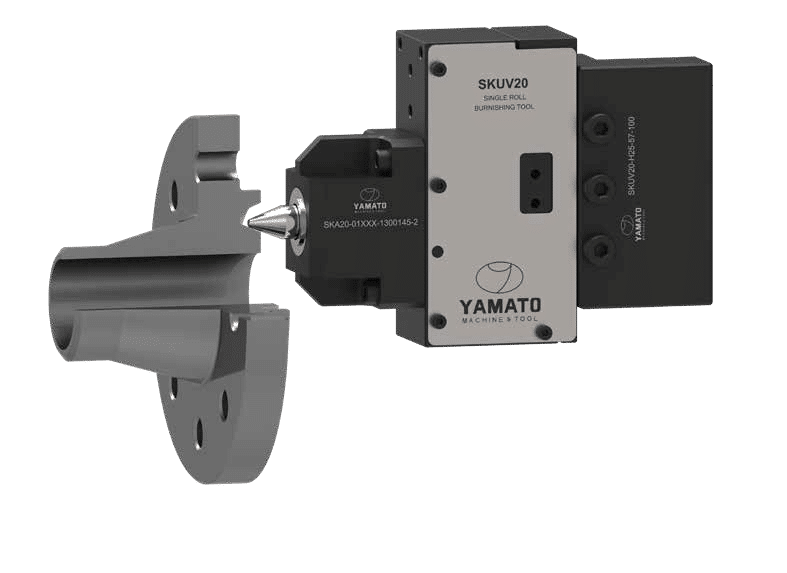
API TOOL SET
2 tools one CNC setup, many different API seal ring diameters
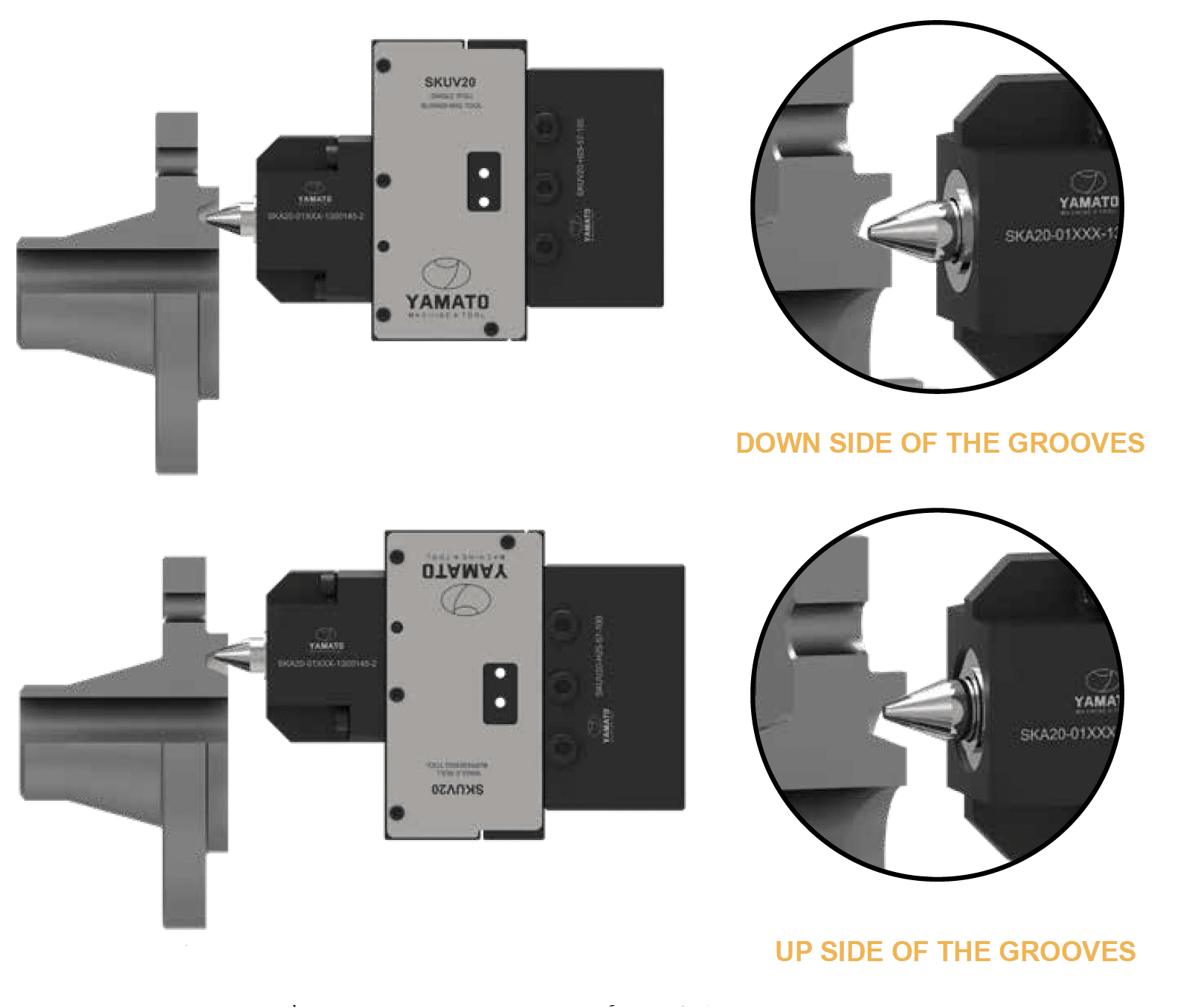
Process advantages and benefits of burnishing
Harder surface – During the extremely fast cycle time for part sizing and finishing, the work surface is also being workhardened and straightened. Surface hardness increases from 20% to 120% with a penetration of 0.2 to 0.75 mm. The low micro finish combined with a hardened and denser surface substantially increases part wear life and corrosion resistance, the added strength improves fatigue resistance, decreasing part failures.
Improved Surface Finish – The burnishing tool works metal without cutting or abrading the surface. It moves the metal, smoothing and compressing the peaks into the valleys, generating a dense and uniform surface – friction free and leaving no feathered edges.